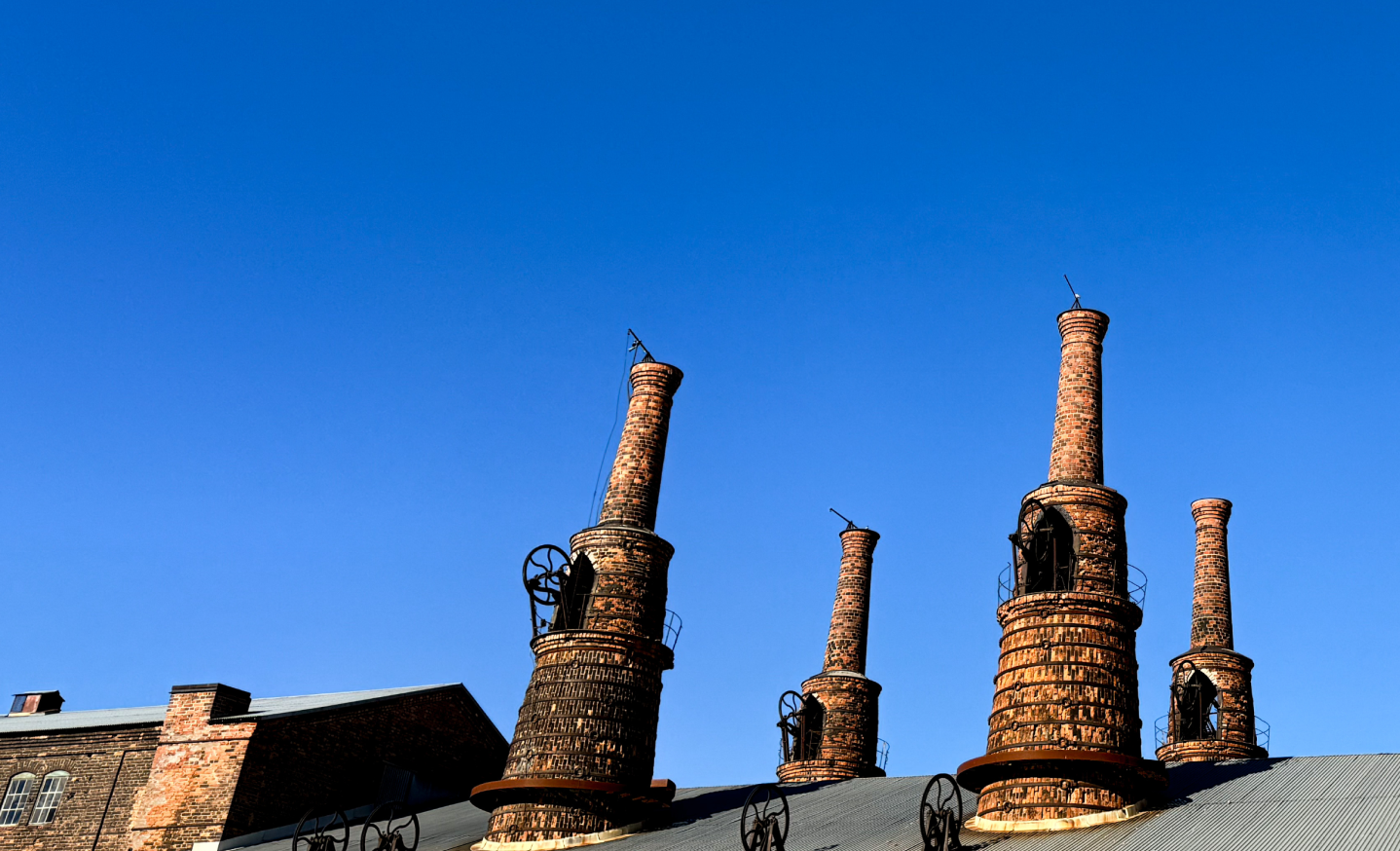
Superior grinding media from Forsbacka Kulverk
Grinding Media
As a supplier of hot-rolled grinding media to a number of the world’s leading mining and recycling customers, our wear-resistant grinding balls and rods are the result of decades of experience meeting the industry’s highest demands.
Controlling the microstructure
Whether wet grinding ore for iron, copper or gold production, or dry grinding recycled glass or softer materials, even the slightest variations in steel chemistry and microstructure can have dramatic impacts on wear resistance.
Superior hardness
This is why, in addition to their superior hardness, our high-carbon grinding balls are rigorously controlled to ensure consistent rolling, tempering and quenching for optimal wear resistance in every batch. Likewise, our tailor-made rod grinders are delivered as rolled, in a wide range of dimensions, with hardness levels up to 688-739 HBW (62-65 HRC). The result is one of the market’s broadest portfolios of supremely robust grinding media, reliably processed, tailored and delivered to guarantee your long-lasting performance.
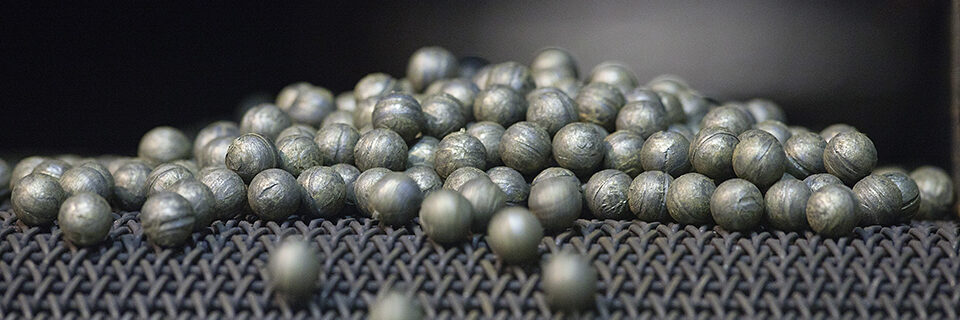
Optimized performance
Forsbacka Kulverk combines know-how in steel making and nearly 100 years of experience manufacturing of grinding media, selecting the right steel grade together with the correct processing and heat treatment parameters in order to optimize performance under different working conditions.
Wear resistance
For a given grinding ball – steel chemistry and micro structure are the dominant factors for controlling wear resistance. Increasing hardness leads to improved wear resistance.
Standard products
- A-810/A-809B, 51CrV4 grinding balls in sizes: 25 –30 –35 –40 –50 –60
- The Balls are delivered quenched and annealed.
- In addition balls can be delivered tumbled or shot blasted and painted.

Applications
Wet grinding for minerals containing
Grinding in cement manufacturing
Grinding of softer minerals/material
Recycling wet/dry grinding
We use 100% green, fossil-free electricity from Gävle Energi
As our electricity supplier, we have chosen Gävle Energi – a local company that supplies renewable electricity from hydroelectric power. It feels extra good to know that we are not only making a climate-smart choice, but also supporting the local community where we operate. Together for a sustainable future in Gävle!
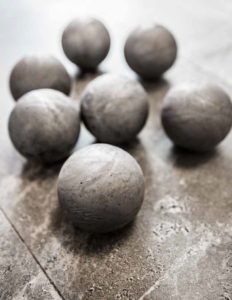
You’ll start to love the daily grind
Grinding balls from Forsbacka Kulverk are used by one of the world’s leading processors of iron ore products in their primary mill, just prior to flotation and magnetic separation. Every month, ton after ton, the grinding media helps them to secure the cost-efficient production of ore pellets renowned for their high purity level.
Superior hardness. Consistent composition. And constant availability under any conditions. Just a few of the properties customers tell us matter most when it comes to our grinding media solutions.
Contact us
Office +46 (0)70 287 31 10
E-mail: sales@kulverket.se
Forsbacka Kulverk
Stentorpsvägen
818 42, Forsbacka
Sweden